Coral Bay Nickel Corporation operates a
Hydrometallurgical Processing Plant (HPP) to
produce nickel and cobalt sulfide from existing stockpiles of low grade nickel
ores from the Rio Tuba nickel mine of Rio Tuba Nickel Mining Corporation.

REQUESTED TOPICS Are The Following:
- Pre-Drying Coal High Moisture Content.
- Opportunities for Compressed-Air Optimization (Key Energy saving areas).
- The 14 R's of compressed air efficiency.
- Waste heat recovery and importance of maintenance.
- Identifying the electrical cost of compressed air.
- Co-generation of energy.
- Recycle of Power (Heat, Steam, Pressure).
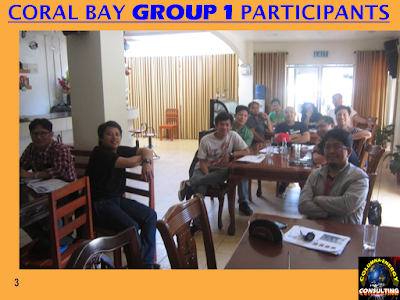
The 14 R’s of Compressor Efficiency
- Reduce leakage losses.
- Reduce pressure at points of use.
- Reduce pressure at source (compressors).
- Reduce system pressure fluctuations using adequately sized and located air receivers and controls.
- Reduce number of partially loaded compressors to only one.
- Remove inappropriate applications.
- Reduce system pressure drop losses with properly sized piping and valves.
- Remove moisture content of compressed air with the proper type and size of dryers.
- Remove condensate without loss of compressed air.
- Reduce downtime through preventive maintenance.
- Record system data and maintenance.
- Review air usage patterns regularly.
- Recover heat.
- Reduce energy costs (return on investment and cost of operation).
A survey of more than 2,000 seminar attendees conducted over a two-year period were asked what situations contribute to Machine Breakdown that are related to Basic Maintenance.
The following Maintenance Basics are precisely where many Maintenance Training Programs fail to focus. Thus, COLUMNA ENERGY CONSULTING included the BASICS highlighted in the survey that fall within the Three (3) main categories:
1. Equipment CLEANLINESS.
2. Proper FASTENING procedures.
3. Proper LUBRICATION procedures.

No comments:
Post a Comment